1、 引言
為了解不同的軋制工藝對TC11鈦合金厚板組織和性能的影響,本章著重從軋制溫度、軋制變形量、軋制換向方式三方面入手對TC11鈦合金厚板的組織與性能開展研究。分析不同的開坯軋制溫度、軋制變形量和軋制換向方式對 TC11鈦合金厚板熱態(tài)以及退火態(tài)組織性能的影響,確定最佳的軋制工藝參數(shù)。本文章采用四輥可逆式 1200mm 熱軋機(jī)參數(shù)如表 3.1 所示。
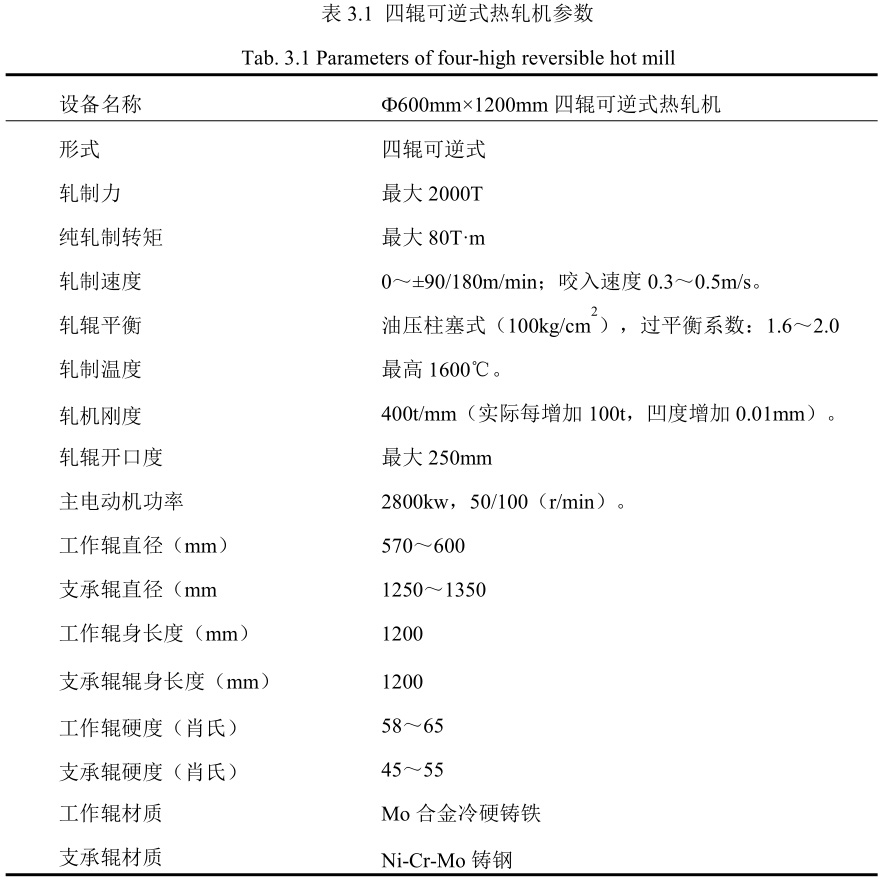
2 、開坯溫度對TC11鈦合金厚板組織及性能影響
為了研究不同的軋制溫度對TC11鈦合金厚板組織和性能的影響,本文采用了兩種不同的軋制溫度對TC11板材進(jìn)行開坯軋制[57],表 3.2 為不同軋制溫度的軋制工藝。
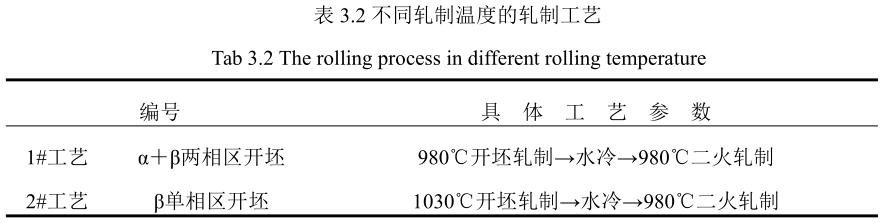
對兩種不同的開坯工藝制得的 40mm 厚TC11板材,分別測試其熱態(tài)的顯微組織及力學(xué)性能,并進(jìn)行對比,研究不同的軋制溫度對TC11厚板熱態(tài)顯微組織的影響,隨后對兩種工藝下制得的板材進(jìn)行 990℃/1h AC+550℃/6h FC 成品熱處理,對比分析兩種工藝對成品TC11板材的組織及性能的影響。
2.1 開坯溫度對TC11鈦合金厚板顯微組織的影響
為研究不同的軋制溫度對TC11鈦合金厚板熱態(tài)顯微組織的影響,對不同軋制溫度的工藝下制得的熱態(tài)板材顯微組織進(jìn)行了觀察。圖 3.1 為經(jīng)兩種不同開坯軋制溫度制得 40mm 厚熱軋板的顯微組織。
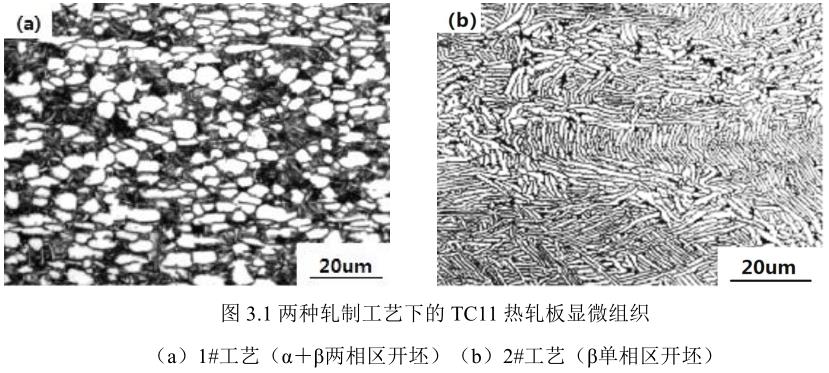
從圖中我們不難看出,不同的開坯溫度對TC11鈦板材的熱態(tài)顯微組織影響很大。板材經(jīng) 1#工藝(α+β兩相區(qū)開坯)軋制后獲得了α+β兩相區(qū)加工組織,板材的顯微組織由等軸的初生α和片層狀的次生α以及β相組成。這是由于在該工藝下,板材兩火軋制均在兩相區(qū)上部開始變形,并終止在兩相區(qū),在變形的過程中發(fā)生動態(tài)回復(fù)與再結(jié)晶。經(jīng)變形后,初生α等軸化,同時,在冷卻的過程中β基體上逐漸析出片層狀的次生α,從而板材獲得了典型的雙態(tài)組織,該組織的綜合力學(xué)性能較好。而板材經(jīng)過 2#工藝(β單相區(qū)開坯)軋制后雖然也獲得了α+β兩相區(qū)加工組織,但組織形貌與 1#工藝截然不同,板材的顯微組織由細(xì)小的網(wǎng)籃組織組成。
這是由于在該工藝下,板材在β單相區(qū)開坯軋制,即板材在單相區(qū)開始變形,變形終止在兩相區(qū)。隨著軋制的溫降,在β晶界處優(yōu)先析出α相,因此晶界α最早承受變形,隨著變形的進(jìn)一步增加,長條的晶界α斷開,形成斷續(xù)的α相,而晶粒內(nèi)部析出的α束集經(jīng)過一定的變形相互交錯,形成編織狀。該類型組織有利于阻礙裂紋擴(kuò)展,提高板材的斷裂韌性和沖擊韌性[65]。
對兩種軋制工藝下獲得的熱態(tài)板材進(jìn)行熱處理,熱處理制度為 990℃/1hAC+550℃/6h FC,對其顯微組織進(jìn)行了觀察。圖 3.2 為經(jīng)兩種不同開坯軋制溫度,兩火軋至 40mm 后,經(jīng) 990℃/1h AC+550℃/6hFC 雙重退火后的顯微組織。
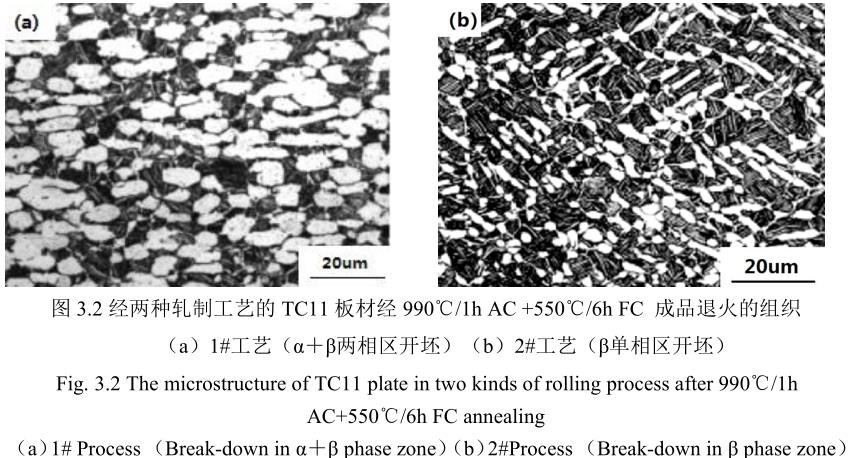
從圖中我們可以看出,兩種工藝下的板材經(jīng)成品退火后,初生α晶粒逐漸等軸化,次生α晶粒條狀化,呈雙態(tài)組織。但也有明顯區(qū)別,1#板材經(jīng)退火后,初生α晶粒在有著明顯長大,經(jīng)檢測,其平均晶粒尺寸為 10~20μm,而 2#板材經(jīng)高溫退火后,α相向β相轉(zhuǎn)變,且編織狀的長條α逐漸等軸化,在后續(xù)時效過程中,β基體中析出次生α,呈條狀分布,初生α晶粒尺寸較 1#工藝板材細(xì)小,約 10μm 左右。
2.2 開坯溫度對TC11鈦合金厚板性能的影響
為研究不同的軋制溫度對TC11鈦合金厚板性能的影響,對不同軋制溫度的工藝下制得的熱態(tài)板材的縱、橫向室溫拉伸和沖擊性能進(jìn)行了測試。表 3.3 為經(jīng)兩種不同開坯軋制溫度軋至 40mm 時熱軋板的縱、橫向力學(xué)性能。
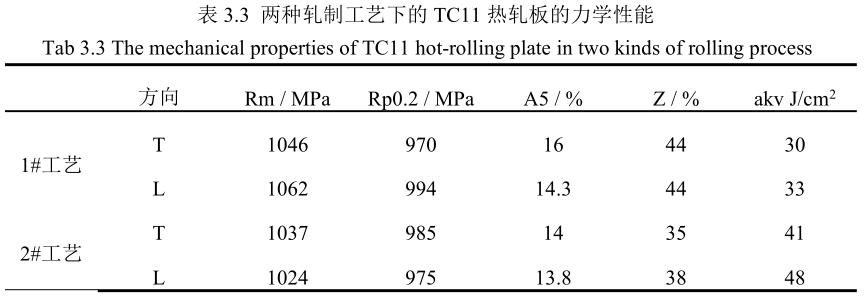
由上表我們不難看出,1#與 2#工藝下板材的縱橫向力學(xué)性能差異均較小,并且 1#工藝的室溫抗拉強(qiáng)度略高于 2#工藝的板材,且延伸率與斷面收縮率明顯優(yōu)于2#工藝的板材,但沖擊性能明顯低于 2#工藝的板材。這是由于開坯溫度不同導(dǎo)致的板材組織不同。一般情況下網(wǎng)籃組織的抗拉強(qiáng)度與沖擊性能優(yōu)于等軸組織,而延伸率偏低。但是優(yōu)于動態(tài)回復(fù)與再結(jié)晶的作用,1#工藝在β基體中存在一定量的片層狀次生α’相。次生α’相一定程度上提升了板材的抗拉強(qiáng)度,但是由于次生α’相過于薄并且體積分?jǐn)?shù)較低,因此對沖擊性能改善不明顯。
對兩種軋制工藝下獲得的熱態(tài)板材進(jìn)行熱處理,熱處理制度為 990℃/1hAC+550℃/6h FC,對其縱、橫向室溫拉伸和沖擊性能進(jìn)行了測試。表 3.4 為經(jīng)兩種不同開坯軋制溫度,兩火軋至 40mm 后,經(jīng) 990℃/1h AC+550℃/6h FC 雙重退火后的力學(xué)性能。
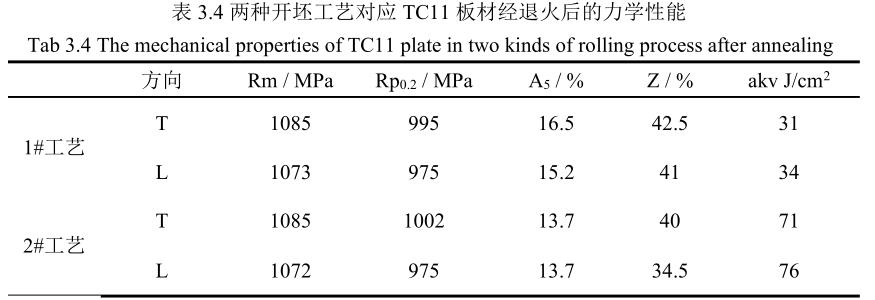
從上表可以看出,經(jīng) 990℃/1h AC+550℃/6h FC 雙重退火后,兩種工藝板材縱橫向力學(xué)性能均較好,較退火前 1#、2#工藝的板材抗拉性能有小幅度提升,1#工藝的延伸率以及 2#工藝的沖擊性能有大幅度提升。1#工藝是由于球狀的亞穩(wěn)定β相繼續(xù)分解,同時片層狀的次生α’相逐漸增厚,并且初生α相繼續(xù)長大所致。而2#工藝的拉長的初生α相逐漸斷裂,然后長大。同時次生α’在拉長的β晶界處生成,因原始的初生α相呈編織狀排列。由于組織的繼承性,退火后的組織也沿原始β晶界程一定編織狀排列,因此極大的提高了材料的沖擊性能。
因此,綜合考慮 1#、2#工藝的熱態(tài)和退火態(tài)的組織和力學(xué)性能以及最終不同狀態(tài)TC11成品的需求量,對于退火態(tài)板材供貨的產(chǎn)品采用 1#工藝進(jìn)行生產(chǎn),對于熱態(tài)交貨的產(chǎn)品采用 2#工藝生產(chǎn)。
3、軋制方式對TC11鈦合金厚板組織及性能影響
由于供貨激光成型用基板的TC11厚板要求網(wǎng)籃組織供貨,而普通TC11厚板要求雙態(tài)組織供貨。編織狀態(tài)的TC11厚板與雙態(tài)組織供貨的TC11厚板均與原始組織編制狀態(tài)有關(guān)。由于同一錠號的板坯數(shù)量有限,為產(chǎn)品交付后的穩(wěn)定性同時節(jié)約材料,本章節(jié)只采用 2#工藝的板材進(jìn)行軋制方式的比對熱軋方式對材料縱橫向力學(xué)性能差異的影響。軋制方式確定前對板坯坐標(biāo)系加以定義,如圖 3.3 所示,方便后文描述。
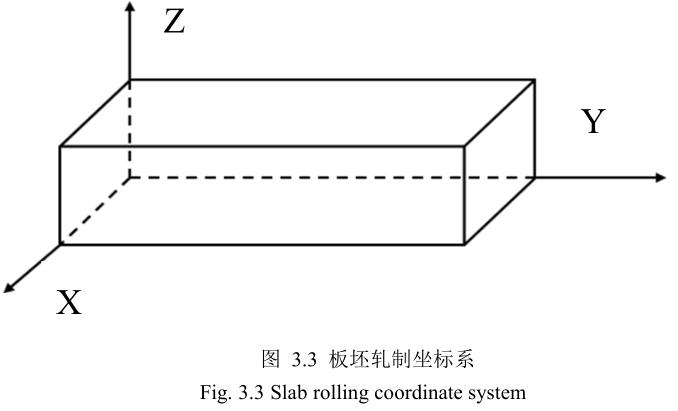
板材的熱軋方式主要有以下五類:
(1)全縱軋法。所謂縱軋就是板材的延伸方向與原料(板坯)縱軸(Y 軸)方向相一致的軋制方法。
(2)全橫軋法,即將板坯進(jìn)行橫軋(沿 X 軸)直至軋成成品。此法只能用于板坯長度大于或等于成品板材寬度時。
(3)綜合軋制法即橫軋—縱軋法。綜合軋制法,一般分為三步,首先縱軋(沿Y 軸)1~2 道次,平整板坯,稱為成型軋制,然后轉(zhuǎn) 90°(沿 X 軸)延伸到所需的板寬,稱為展寬軋制。然后再轉(zhuǎn) 90°(沿 Y 軸)進(jìn)行縱軋成材,稱為延伸軋制。
(4)角軋—縱軋法。所謂角軋就是將軋件縱軸與軋輥軸線成一定角度(與 Y軸成一定角度)送入軋輥進(jìn)行軋制的方法。
(5)縱橫軋制法。即先沿板坯的縱軸(Y 軸)軋制較大的變形量到一定程度,通過剪切下料的方式垂直于開坯軋制方向切出板材寬度,再換向 90°進(jìn)行以后的軋制的方法。
就這五類軋制法進(jìn)行分析,(4)由于采用一定角度換向,幾何損失大,批次穩(wěn)定性控制難度大,在現(xiàn)代工廠軋制中已經(jīng)很少用到,一般在軋制寬幅較大的板材過程中,如出現(xiàn)板材延長度方向上的不均勻形變,或者來板坯厚度較大時,在軋制過程道次中間選擇采用,本研究中不考慮。
(1)~(2)都是始終沿著一個方向軋制,各向異性必然最大,成品板材縱向變形量最大,因此縱向一般情況下優(yōu)于橫向。本章節(jié)將(1)、(2)合并,考慮為一種軋制方式。(3)、(5)由于存在縱、橫兩個方向的變形,考慮到成品板材厚度 40mm 制定出如圖 3.4 工藝方案。
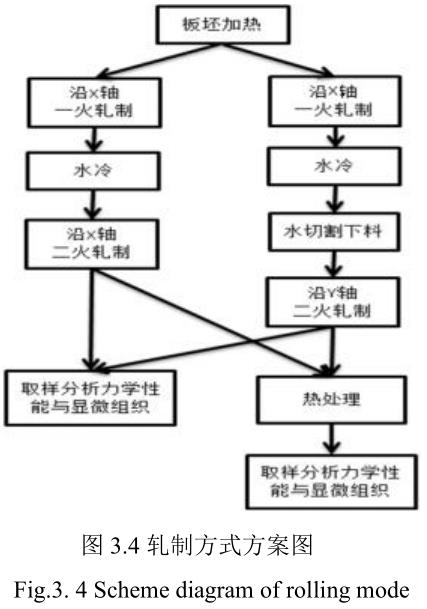
實(shí)驗(yàn)方案:
工藝 A:熔煉→鍛造→板坯加熱(單相區(qū))→熱軋(沿 X 軸)至 90mm→水冷→二火加熱(兩相區(qū))→熱軋(沿 X 軸)42mm→熱矯→表面處理(水磨)→熱態(tài)取樣→成品熱處理取樣分析。
工藝 B:熔煉→鍛造→板坯加熱(單相區(qū))→熱軋(沿 X 軸)至 90mm→水冷→切寬 1040mm(中斷)→二火加熱(兩相區(qū))→熱軋(沿 Y 軸)42mm→熱矯→表面處理(水磨)→熱態(tài)取樣→成品熱處理取樣分析。
3.1 軋制方式對TC11鈦合金厚板顯微組織的影響
將兩種工藝方案的不同方向變形量列表 3.5 如下:
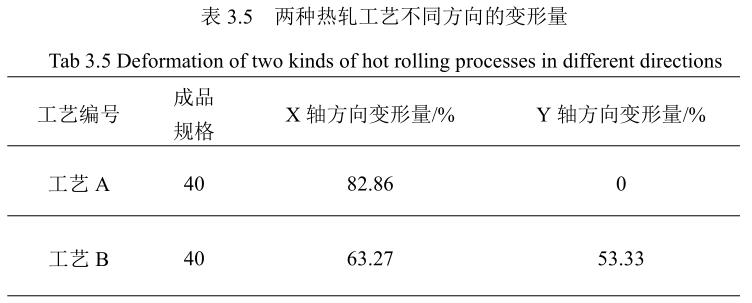
軋制到 40mm 板材后板材的熱態(tài)顯微組織如圖 3.5 所示,退火態(tài)下的縱橫向顯微組織如圖 3.6 所示。
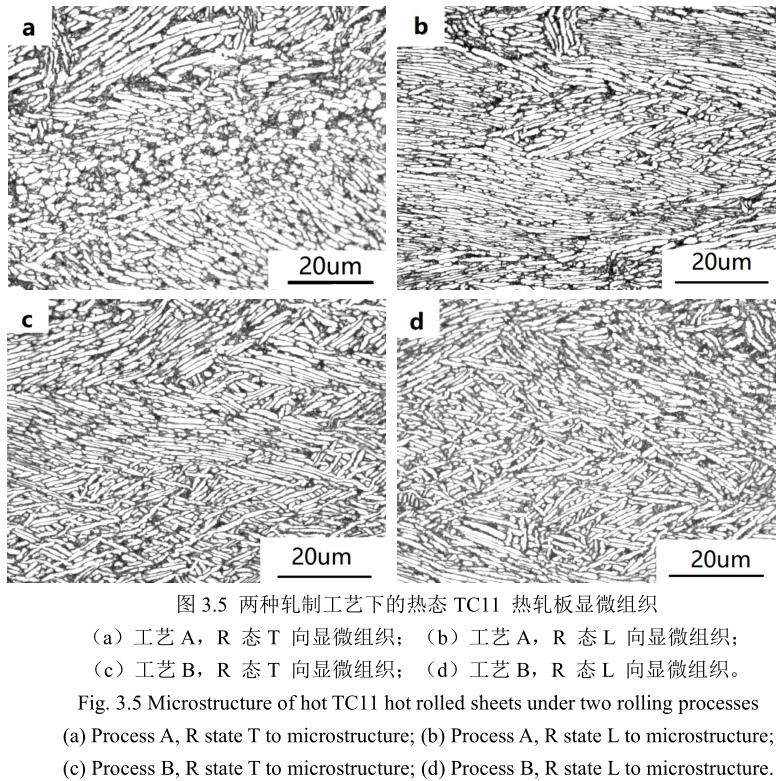
由圖 3.5 可以看出,熱態(tài)的兩種工藝下,組織均為由少量等軸的α相和拉長呈編織狀的α相以及殘余β相組成的網(wǎng)籃組織。圖 3.5(a)橫向組織由于此方向一直未發(fā)生形變,因此等軸的α相比例稍高。但是從縱向 3.5(b)中可以看出此方向晶粒明顯被拉長,在高溫變形過程中,發(fā)生動態(tài)回復(fù)再結(jié)晶,新生成的α相明顯有拉長并沿伸長的β晶界處富集。此時的位錯能相對較高。從形貌上看,新生成的拉長的α晶粒縱橫比一般為 10~20。而圖 3.5(c)可以明顯看出晶粒尺寸大于圖(a),這是由于板材在橫向上先發(fā)生大量變形,在變形過程中更早的發(fā)生動態(tài)回復(fù)與再結(jié)晶,優(yōu)先生成的再結(jié)晶晶核長大時間較長,長大更為充分所致,從圖紙形貌上觀察縱橫比約為 7~10。圖 3.5(d)為工藝 B 的熱態(tài)縱向顯微組織,從圖中可以發(fā)現(xiàn)其晶粒尺寸稍大于全橫向軋制工藝。但是新生成的拉長的α晶粒縱橫比略小于工藝 A,同時β相比例稍高于工藝 A。這是由于縱向累積變形量小于 A工藝所致。尤其在二火軋制過程中,工藝 A 雖然縱向總變形量為 80%,但是先發(fā)生接近 50%的變形量,并充分冷卻后再發(fā)生 57%左右的變形量。這對式樣的縱向拉伸性能影響十分巨大。
兩 種 軋 制 工 藝 下 獲 得 的 熱 態(tài) 板 材 進(jìn)行 熱 處 理, 熱 處 理制 度 為 990 ℃/1hAC+550℃/6h FC,退火后顯微組織如圖 3.6 所示。
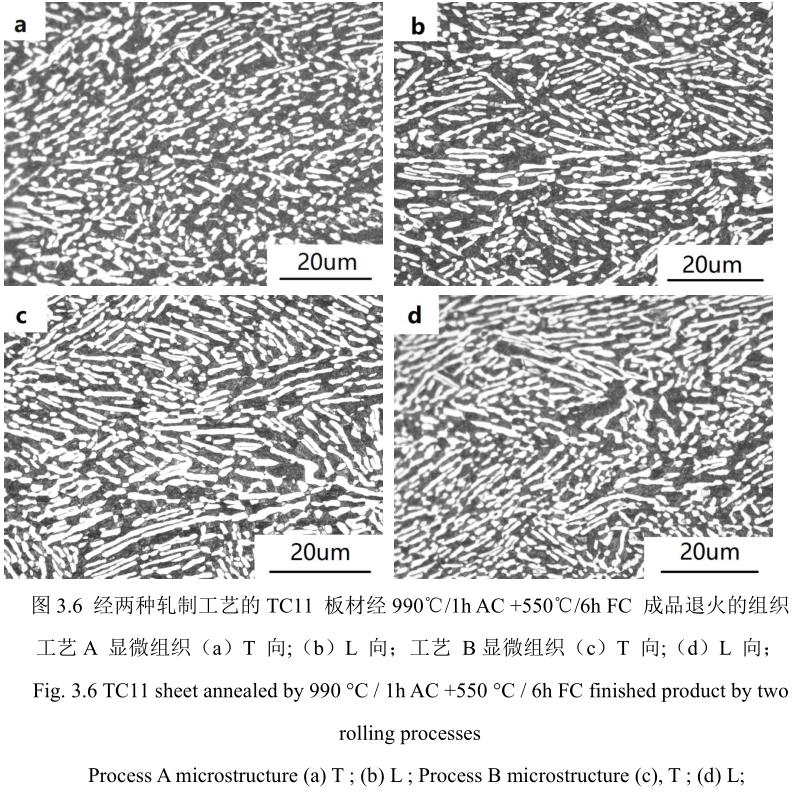
從圖 3.6 中我們可以看出,兩種工藝下的板材經(jīng)成品退火后,初生α晶粒逐漸斷裂開來(等軸化),次生α晶粒條狀化,呈雙態(tài)組織,并且晶粒有長大趨勢。
同時其顯微組織與原始初生α晶粒的形貌息息相關(guān)。兩種工藝的顯微組織也有明顯區(qū)別,A 工藝板材經(jīng)退火后,初生α晶粒比例略低于 B 工藝,同時隨著固溶時效退火的進(jìn)行,初生α晶粒比例低于熱態(tài)組織,殘余β晶粒與次生α晶粒交錯形成在原始β晶界處。工藝 B 板材經(jīng)高溫退火后,α相向β相轉(zhuǎn)變,且編織狀的長條α逐漸等軸化,在后續(xù)時效過程中,β基體中析出次生α,呈條狀分布。同時可以明顯的看出工藝 B 的縱橫向顯微組織差異更小。
3.2 軋制方式對TC11鈦合金厚板力學(xué)性能的影響
為研究不同的軋制方式對TC11鈦合金厚板性能的影響,對不同軋制工藝下制得的熱態(tài)板材的縱、橫向室溫拉伸和沖擊性能進(jìn)行了測試。表 3.6 為經(jīng)兩種不同軋制工藝軋至 40mm 時熱軋板的縱、橫向力學(xué)性能。
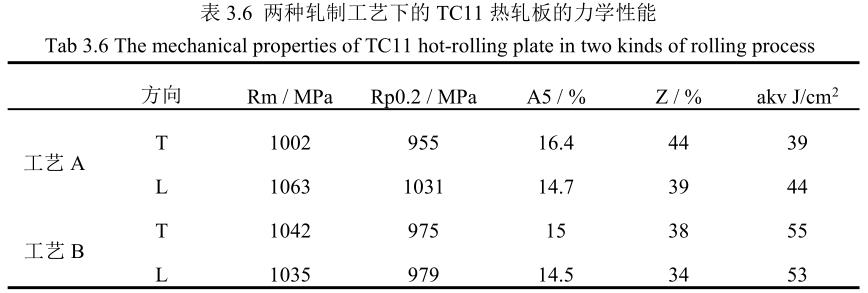
對兩種軋制工藝下獲得的熱態(tài)板材進(jìn)行熱處理,熱處理制度為 990℃/1hAC+550℃/6h FC,對其縱、橫向室溫拉伸和沖擊性能進(jìn)行了測試。表 3.7 為經(jīng)兩種不同軋制工藝,兩火軋至 40mm 后,經(jīng) 960℃/1h AC+550℃/6h FC 雙重退火后的力學(xué)性能。
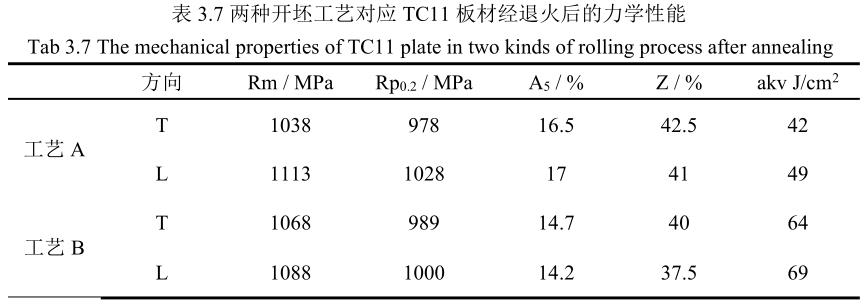
從表 3.6 和 3.7 中可以看出,工藝 A 由于兩火次變形均沿一個方向發(fā)生形變,導(dǎo)致力學(xué)性能差異巨大,各項異性明顯。縱橫向力學(xué)性能差值近 70MPa。而工藝B 由于兩個方向均存在較大程度的變形各向異性減弱,縱橫向力學(xué)性能差值為20MPa 左右。工藝 A 的橫向力學(xué)性能較差,但是工藝 A 的 L 向力學(xué)性能較為優(yōu)異,延伸率也較好。這與縱橫向變形不均勻有直接關(guān)系。退火前后工藝 B 的沖擊性能均高于工藝 A,A 延伸率也優(yōu)于工藝 B,從顯微組織可以明顯看出,由于工藝 A 的組織更為等軸化,工藝 B 片層狀的晶粒以及退火后生成的片層狀的次生α晶粒相對沖擊裂紋的擴(kuò)展起到阻礙以及改變路徑增加了吸收的能量。因此在退火后對材料的沖擊性能均有較大幅度的改善。
4、 開坯變形量對TC11鈦合金厚板組織及性能影響
為了研究不同的軋制變形量對TC11鈦合金厚板組織和性能的影響,本文選用表 3.1 中 2#工藝(β單相區(qū)開坯),并采用了三種不同的軋制變形量對TC11板材進(jìn)行開坯軋制。表 3.8 為不同軋制變形量的軋制工藝。
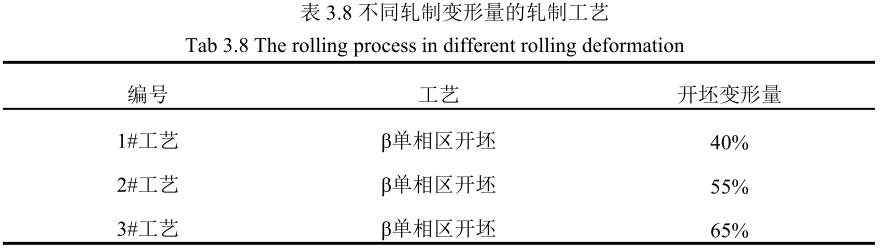
對三種不同的軋制變形量工藝制得的 40mm 厚TC11板材,分別測試其熱態(tài)的顯微組織及力學(xué)性能,并進(jìn)行對比,研究不同的軋制變形量對TC11厚板熱態(tài)顯微組織的影響,隨后對該三種工藝下制得的板材進(jìn)行 990℃/1h AC+550℃/6h FC成品熱處理,對比分析三種工藝對成品TC11板材的組織及性能的影響。
4.1 開坯變形量對TC11鈦合金厚板顯微組織的影響
為研究不同的軋制變形量對TC11鈦合金厚板熱態(tài)顯微組織的影響,對不同軋制變形量的工藝下制得的熱態(tài)板材進(jìn)行顯微組織進(jìn)行了觀察。圖 3.7 為相同TC11 坯料經(jīng)三種不同軋制變形量軋制到 40mm 時熱軋板的顯微組織。
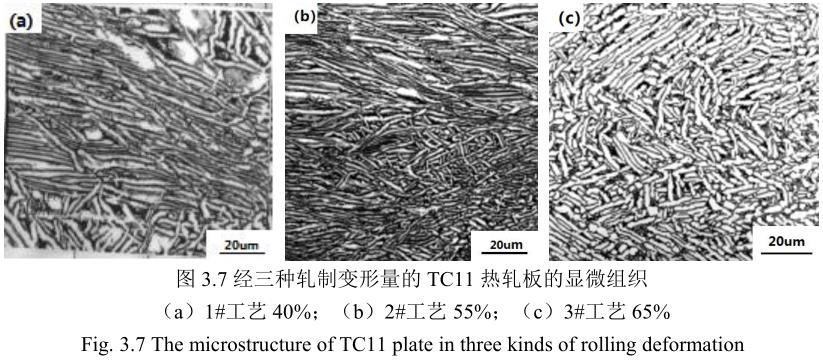
從圖中我們可以看出不同的開坯變形量對成品板材熱態(tài)組織影響很大。當(dāng)開坯變形量為 40%時,板材獲得長條α和局部網(wǎng)籃組織,當(dāng)開坯變形量增大至 55%時,形成不均勻的網(wǎng)籃組織,此時長條α仍較多,而當(dāng)開坯變形量繼續(xù)增大至 65%時,板材獲得了均勻的編織狀網(wǎng)籃組織。這是由于變形量較小時,晶粒內(nèi)部的α束集未完全發(fā)生變形,隨著變形量增大,長條α發(fā)生扭曲變形,不同方向的長條α相互交錯,呈編織狀態(tài),因此網(wǎng)籃組織越均勻。所以,在單相區(qū)加熱并開始軋制,同時開坯軋制時變形量控制在 60%左右時,板材可獲得均勻的網(wǎng)籃組織。
對三種軋制工藝下獲得的熱態(tài)板材進(jìn)行熱處理,熱處理制度為 990℃/1hAC+550℃/6h FC,對其顯微組織進(jìn)行了觀察。圖 3.8 為經(jīng)三種不同軋制工藝,兩火軋至 40mm 后,經(jīng) 990℃/1h AC+550℃/6h FC 雙重退火后的顯微組織。
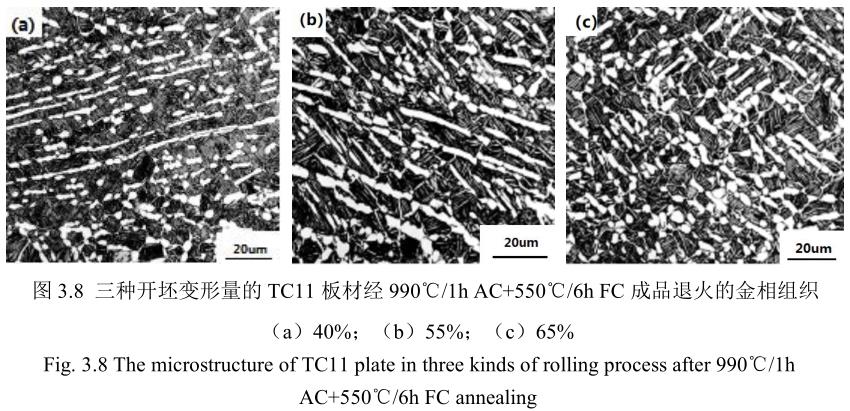
從圖中我們不難看出,三種軋制工藝下獲得的板材經(jīng)成品雙重退火后均得到雙態(tài)組織。但開坯變形量為 40%的板材經(jīng)退火后形成有大量長條α存在的雙態(tài)組織,而當(dāng)開坯變形量增大至 55%的板材經(jīng)退火后獲得了不均勻的雙態(tài)組織,長條α仍然存在,當(dāng)開坯變形量為 65%時,板材經(jīng)退火后獲得均勻的雙態(tài)組織,晶粒尺寸細(xì)小。
對比TC11鈦合金板材的熱態(tài)和退火態(tài)組織發(fā)現(xiàn),其組織有良好的傳承性,均勻的網(wǎng)籃組織經(jīng)雙重退火后得到的雙態(tài)組織非常均勻,晶粒尺寸細(xì)小。
4.2 開坯變形量對TC11鈦合金厚板性能的影響
為研究不同的軋制變形量對TC11鈦合金厚板性能的影響,對不同軋制變形量的工藝下制得的熱態(tài)板材的縱、橫向室溫拉伸和沖擊性能進(jìn)行了測試。表 3.9為經(jīng)三種不同軋制工藝軋至 40mm 時熱軋板的縱、橫向力學(xué)性能。
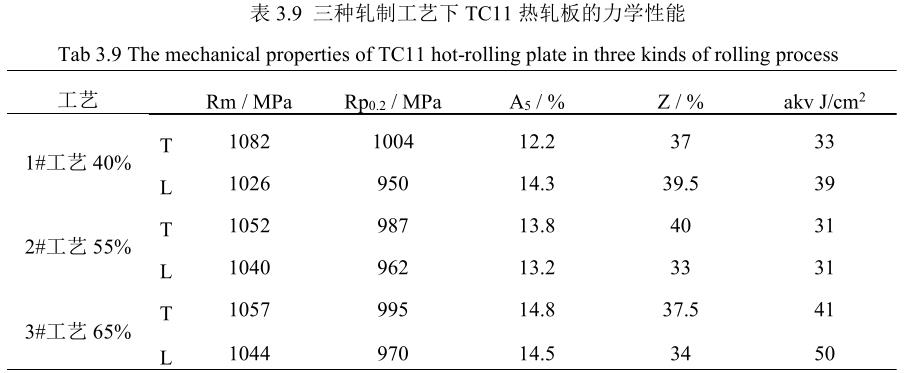
從表中可以看出:三種軋制工藝下,板材的抗拉強(qiáng)度均能達(dá)到 1020MPa 以上,延伸率達(dá)到 13%,沖擊韌性大于 30 J/cm2 。隨著開坯變形量的增加, TC11熱態(tài)板材的縱、橫向性能差異逐漸變小,這主要是由于網(wǎng)籃組織隨著變形的增加而變形均勻;同時,隨著開坯變形量的增加,TC11 板材熱態(tài)沖擊韌性逐漸提高,這是因?yàn)殚_坯變形量越大,板材獲得更加均勻的網(wǎng)籃組織,編織狀交錯的α相有阻礙裂紋擴(kuò)展的特性。
對三種軋制工藝下獲得的熱態(tài)板材進(jìn)行熱處理,熱處理制度為 990℃/1hAC+550℃/6h FC,對其縱、橫向室溫拉伸和沖擊性能進(jìn)行了測試。表 3.10 為經(jīng)三種不同軋制工藝,兩火軋至 40mm 后,經(jīng) 990℃/1h AC+550℃/6h FC 雙重退火后的縱、橫向力學(xué)性能。
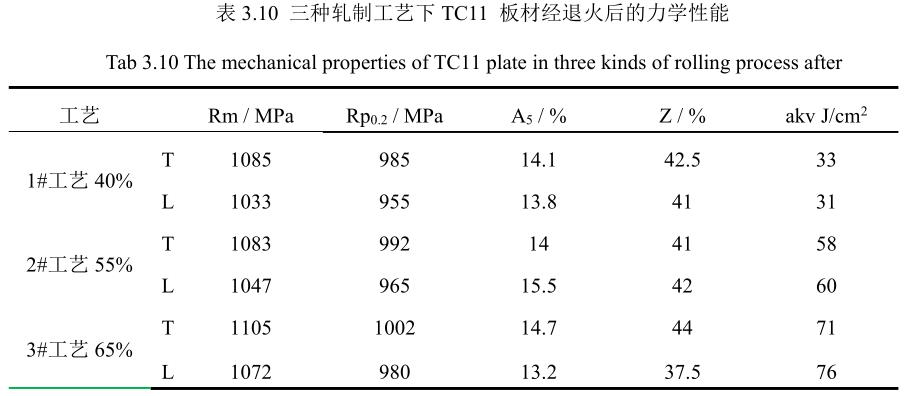
從上表可以看出,經(jīng) 990℃/1h AC+550℃/6h FC 雙重退火后,三種工藝下的板材強(qiáng)度和沖擊韌性有了大幅提升,塑性也有所提高。這是由于經(jīng)退火后,網(wǎng)籃組織轉(zhuǎn)變成了雙態(tài)組織,大量的片層狀次生α相,提高了材料的強(qiáng)度,也利于材料的沖擊性能。且隨著開坯變形量的增加,板材的縱、橫向性能差異逐漸變小;同時,隨著開坯變形量的增加,TC11 板材強(qiáng)度和沖擊韌性逐漸提高,這是因?yàn)殚_坯變形量越大,板材獲得更加均勻的網(wǎng)籃組織,經(jīng)退火后獲得細(xì)小的雙態(tài)組織,細(xì)小的等軸組織有利于提高材料的強(qiáng)度,細(xì)小的片層狀次生α有阻礙裂紋擴(kuò)展的特性,從而提高板材的沖擊性能。
由于本研究涉及企業(yè)的新產(chǎn)品開發(fā)技術(shù),根據(jù)企業(yè)技術(shù)保密協(xié)議和訂貨商合同要求,研究中的部分工藝參數(shù)不能詳細(xì)表述,僅做相關(guān)原則說明。
4.3 開坯變形量對TC11鈦合金厚板不同厚度位置顯微組織的影響
由于設(shè)備能力有限,熱軋厚板在開坯軋制過程中的實(shí)際單道次壓下量有限,軋制過程的變形總是會從板坯的表層逐漸滲透到板材心部,為保證板材厚度方向上的組織一致性,必要保證材料的道次變形量和總變形量。但是實(shí)際工業(yè)生產(chǎn)過程中,由于在軋制過程中的溫降,板坯表面和邊部降溫尤其快,隨著溫度的下降材料的塑性明顯降低,這個時候如果繼續(xù)大變形量變形會導(dǎo)致材料表面和邊部開裂,使成品率下降,或產(chǎn)生廢品。因此選擇一個合適的經(jīng)濟(jì)實(shí)用的變形量對于厚板的工業(yè)化生產(chǎn)十分必要。圖 3.9、3.10、3.11 分別反映開坯變形量為 40%、55%、65%變形量面材料表層與中心層的這種差異圖。
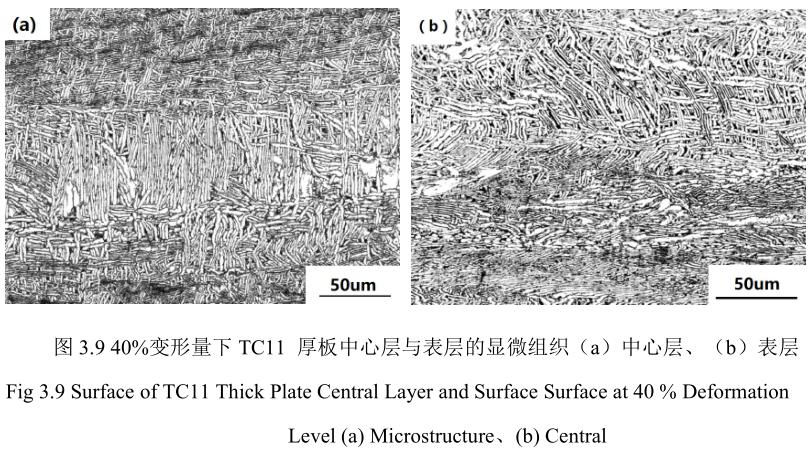
上圖為開坯 40%變形量下TC11中心層與表層的顯微組織,為增大視野,更多的暴露出高向上的形變差異帶來的組織差異,選用 200 倍顯微組織圖作為比對。可以在圖 a 中間明顯看見高向上未完全破碎的原始α晶粒。區(qū)間范圍為中心層約 100~150μm。這種未破碎的拉長狀組織縱橫比一般為 0.1,甚至更多,這與上下表層發(fā)生變形后的長條狀α晶粒縱橫比一般為 7~20 呈現(xiàn)出巨大差異,為這會對材料的拉伸性能帶來巨大影響。
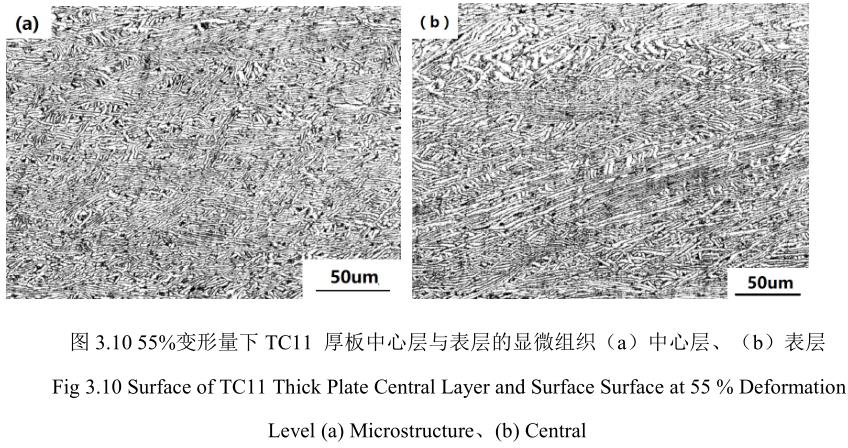
上圖為開坯 55%變形量下TC11中心層與表層的顯微組織,從上圖中可以明顯看出,在高度方向上,不同位置的板材均發(fā)生較好變形,晶粒破碎充分。初生的α晶粒呈略微拉長狀態(tài)。并且縱橫比總體小于圖 3.9 中 40%變形量下的縱橫比。
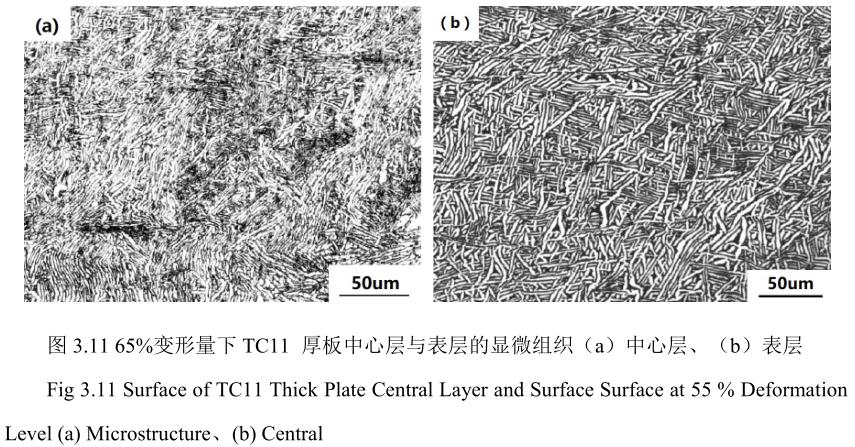
上圖為開坯 65%變形量下TC11中心層與表層的顯微組織,圖 a 我們可以明顯看出表層顯微組織明顯粗化,同時中心層局部地區(qū)出現(xiàn)出現(xiàn)β斑,這是由于變形量過大心部溫度上升過快,使局部溫度過高導(dǎo)致。適當(dāng)?shù)慕档蛙堉扑俣瓤梢杂行Ц纳凭植窟^熱現(xiàn)象。但是降低了軋制速度會導(dǎo)致材料表面及邊部的溫度大幅度下降,這在后續(xù)軋制過程中極易出現(xiàn)表面裂紋或裂邊現(xiàn)象。如圖 3.12 所示。
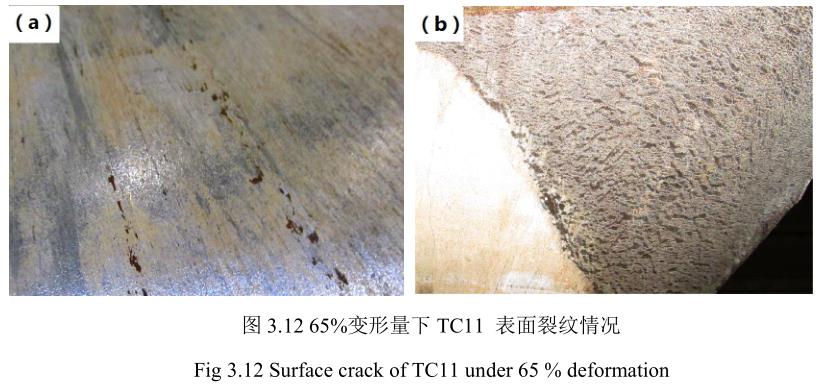
因此綜上所述,TC11鈦合金的開坯變形量最好控制在 55%~60%之間,變形量過小不利于變形深入到板材內(nèi)部,而變形量太大軋制時間過長又容易出現(xiàn)板面裂紋和心部過熱現(xiàn)象,如生產(chǎn)上必須采用更大的變形量時,適當(dāng)降低軋制速度同時進(jìn)行回爐再加熱的方式進(jìn)行軋制,由于具體軋制壓下及回爐再加熱工藝設(shè)計,涉及我公司TC11組織控制專有技術(shù),本文不作相關(guān)描述。
相關(guān)鏈接