鈦合金由于具有比重小、比強(qiáng)度高以及優(yōu)良的抗腐蝕性能的優(yōu)點(diǎn),在航空航天、船舶以及醫(yī)療等許多方面得到了運(yùn)用。尤其隨著最近冶煉技術(shù)與加工制造業(yè)的迅猛發(fā)展,鈦合金材料在航空航天領(lǐng)域的運(yùn)用也越來(lái)越廣泛。在軍機(jī)上鈦合金的使用量越來(lái)越大,最近幾年為減輕飛機(jī)重量很多結(jié)構(gòu)件都采用了鈦合金,蘇—27飛機(jī)上各種鈦合金零件的總質(zhì)量約占飛機(jī)總質(zhì)量的15%。
鈦合金具有較高的缺陷敏感性,其冶煉缺陷主要有金屬夾雜、非金屬夾雜、化學(xué)成分偏析,其中偏析出現(xiàn)的機(jī)率較高。然而,由于材料檢驗(yàn)抽樣的隨機(jī)性使得有些缺陷并不能在材料檢 驗(yàn)中均被檢出,這些缺陷可能會(huì)在生產(chǎn)加工、熱處理等過(guò)程中才暴露出來(lái)。另外由于鈦合金發(fā)展使用的歷史較短,目前對(duì)鈦合金的研究遠(yuǎn)不如對(duì)鋼合金與鋁合金等的研究深入,參考資料也相對(duì)較少,因此為了提高鈦合金的冶煉質(zhì)量與零件使用及其工作的可靠性,在生產(chǎn)實(shí)踐中研究鈦合金的宏觀、微觀組織及其對(duì)力學(xué)性能的影響有著重要的意義。
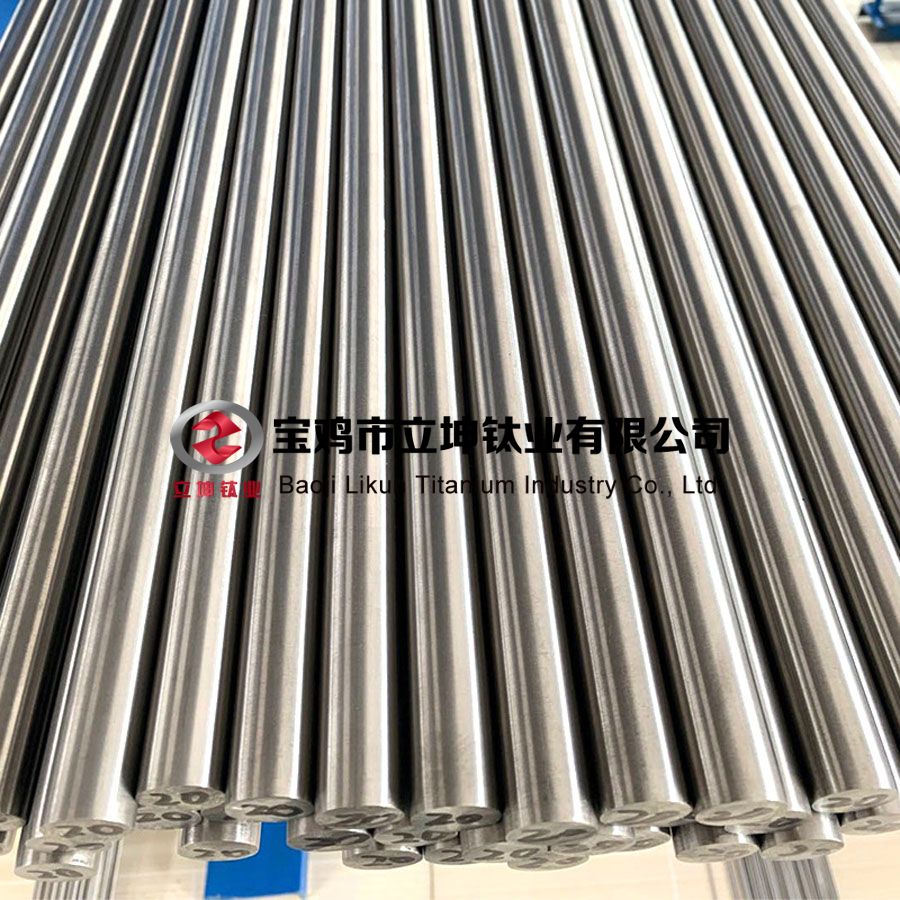
近幾年為了減輕彈射座椅的質(zhì)量,部分零件已經(jīng)開 始 使 用 鈦 合 金。 某 型 彈 射 座 椅 用Φ 55mmTC11鈦合金熱軋棒料在900℃真空退火90min后表面出現(xiàn)了縱裂紋,裂紋斷續(xù)沿縱表面分布。為了查明裂紋產(chǎn)生的原因,實(shí)驗(yàn)對(duì)開裂的TC11鈦合金棒進(jìn)行了理化檢驗(yàn)和分析。
TC11鈦合金棒在退火后發(fā)現(xiàn)裂紋。為分析裂紋產(chǎn)生的原因,對(duì)其進(jìn)行了裂紋宏觀和微觀檢驗(yàn)、顯微硬度測(cè)試和能譜分析。結(jié)果表明:原材料在冶煉過(guò)程中氧、碳含量偏高聚集在材料中形成偏析,在軋制過(guò)程中開裂,退火后發(fā)現(xiàn)的鈦棒縱表面的裂紋是由原材料帶來(lái)的。
1、理化檢驗(yàn)
1.1 宏觀檢驗(yàn)
開裂鈦合金棒的宏觀形貌如圖1所示,可見(jiàn)裂紋在棒料外表面沿縱向間斷分布。圖2為橫向取樣的宏觀形貌,可見(jiàn)裂紋深達(dá) 3.6mm,尾端圓鈍,并不尖銳。
1.2 微觀檢驗(yàn)
圖3~5是從同一裂紋沿縱表面取樣磨制侵蝕后在不同部位獲得的顯微組織形貌,可以清楚的看到裂紋附近有一條白亮條帶狀組織,白亮區(qū)與基體組織邊界分明。但白亮區(qū)并未與基體完全剝離,一邊與基體結(jié)合成為 一體。棒料從 白 亮條帶一 側(cè) 開裂,裂紋一側(cè)為基體組織,另一側(cè)為白亮區(qū)。白亮條帶與基體組織明顯不同。由圖5可見(jiàn),裂紋在白亮條帶尾端附近終止。裂紋是白亮條帶的一側(cè)與基體分離而產(chǎn)生。白亮區(qū)寬度約0.3mm。由此可見(jiàn),裂紋的產(chǎn)生與白亮條帶的存在應(yīng)該有很大的關(guān)系。
圖1 縱表面裂紋的宏觀形貌
1.3 顯微硬度測(cè)試
白亮區(qū)為富氧α組織,對(duì)白亮條帶與基體進(jìn)行顯微硬度試驗(yàn),試驗(yàn)載荷為200g。測(cè)得白亮條帶處的顯微硬度為550,572,532,560HV0.2,平均值為560HV0.2;基 體 的 顯 微 硬 度 為438,446,442,434HV0.2,平均值為440HV0.2。條帶處的顯微硬度比基體處的高出約30%,由圖6也可以看出,白亮條帶的顯微硬度壓痕比基體的小。
圖7是裂紋橫截面的顯微組織,可見(jiàn)左下側(cè)的白亮組織(α相)明顯比右上側(cè)的多。圖8是基體的顯微組織,可見(jiàn)為α+β等軸組織。等軸組織的特點(diǎn)是等軸狀的α相分布在轉(zhuǎn)變了的β相基體上,等軸組織有著很好的拉伸塑性和疲勞強(qiáng)度。圖9是橫截面處的微裂紋形貌,可見(jiàn)主裂紋邊緣出現(xiàn)了分支微裂紋。
1.4 能譜分析
對(duì)白亮區(qū)利用能譜進(jìn)行微區(qū)成分分析,結(jié)果如圖10所示,可見(jiàn)缺陷中氧與碳的含量很高。
2、分析與討論
通常由于熱處理不當(dāng)導(dǎo)致零件(或材料)產(chǎn)生的裂紋通常尾端尖銳,呈擴(kuò)展態(tài)勢(shì),圖2顯示,裂紋尾部并不尖銳,也無(wú)擴(kuò)展特征。在圖3~5中,白亮條帶只出現(xiàn)在裂紋的一側(cè),且在圖6中可見(jiàn),條帶缺陷
處的顯微硬度壓痕比基體處的小,條帶處的顯微硬度比基體處的高出約30%。由此說(shuō)明白亮條帶與基體差異極大。
通常退火致裂的情況極少。棒料進(jìn)廠后只進(jìn)行了退火處理,并無(wú)其他后續(xù)工序,則裂紋應(yīng)是由原材料帶來(lái)的。若氧與碳的含量明顯偏高是由退火造成的,出現(xiàn)污染,那么白亮條帶應(yīng)該出現(xiàn)在裂紋兩邊,從圖3~5可以看出白亮條帶只出現(xiàn)在裂 縫一側(cè)。
據(jù)此,裂縫是原材料的折疊或拉痕的可能性也可以排除。且由圖1和圖2可見(jiàn),裂紋宏觀上尾部并不尖銳,不具備熱處理裂紋的特征。故可知富碳、氧的亮條是由原材料自身帶來(lái)的,也就是說(shuō)裂紋是由原材料帶來(lái)的。
陶春 虎 等 人 也 曾 對(duì) 此 類 白 亮 條 帶 進(jìn) 行 過(guò) 分析,結(jié)果證明該缺陷為富氧與富碳α層,為富α偏析。該缺陷的存在是由于鈦錠熔煉時(shí)合金中富含氧與碳,導(dǎo)致材料脆化,使得缺陷處顯微硬度比基體部位的高。
白亮區(qū)并未與基體完全剝離,一邊與基體結(jié)合成為一體,應(yīng)該不是夾雜,而是氧與碳聚集產(chǎn)生的偏析。裂紋是在白亮條帶尾端附近終止且在白亮條帶的一側(cè)與基體分離,因此裂紋與白亮條帶的存在有很大關(guān)系,而白亮條帶中碳、氧含量明顯偏高。白亮區(qū)為富氧α組織,白亮區(qū)中α相明顯偏高。圖9的偏析區(qū)中出現(xiàn)了細(xì)小的微裂紋。
能譜分析結(jié)果表明,雜 質(zhì)元 素氧、碳 的 含 量 偏高,氧、碳聚集在材料中形成了偏析。氧、碳提高相變點(diǎn),擴(kuò)大α相區(qū),穩(wěn)定α組織,這使得組織中出現(xiàn)了α亮條帶。富α組織能使強(qiáng)度、硬度大幅提高,但
塑性、斷裂韌度以及抗蠕變性能急劇下降,這是亮條區(qū)硬度偏高的原因。
富氧α層的顯微硬度較高,塑性變形能力差,從而使材料的脆性增加,脆性較大能促使裂紋的形成與發(fā)展。這樣棒料在軋制過(guò)程中就有開裂的可能。同時(shí)產(chǎn)生偏析必然導(dǎo)致材料體積范圍內(nèi)的性能不均勻,從而會(huì)降低材料的力學(xué)性能,尤其是界面兩側(cè)的變形不協(xié)調(diào)導(dǎo)致局部應(yīng)力的提高,使疲勞裂紋易于萌生。
偏析產(chǎn)生的原因是由于合金中雜質(zhì)元素或合金元素局部聚集而形成的,會(huì)使組織中出現(xiàn)α亮斑、亮條或β斑。
β斑即為β偏析,β偏析的產(chǎn)生原因是合金冶煉在凝固的過(guò)程中同一溫度下的固相成分和液相成分有差別,液相總是含有比固相更多的β穩(wěn)定元素,從而導(dǎo)致比較容易產(chǎn)生鑄錠中心和頭部的β穩(wěn)定元素的 偏 析,一般出 現(xiàn) 在鑄錠 的 等軸區(qū)域。β斑對(duì)拉伸性能、熱穩(wěn)定性、斷裂韌度、低周疲勞和高周疲勞性能會(huì)產(chǎn)生極其不利的影響。β斑常常是裂紋的起源,對(duì)壽命的影響也較大。
偏析在材料檢驗(yàn)中可以通過(guò)低倍試驗(yàn)發(fā)現(xiàn)。試樣在常溫的強(qiáng)酸溶液里腐蝕(通常用工業(yè)純體積分?jǐn)?shù)為13%~17%的 硝酸與8.5%~13.5%的 氫氟酸,或者化 學(xué) 純 體 積 分 數(shù) 為13% ~17% 的 硝 酸 與10.5% ~13.5%的 氫 氟 酸 ),約 腐 蝕 掉 0.05~0.10mm的厚度后立即在干凈的水中清洗并吹干,然后進(jìn)行觀察。偏析將在無(wú)光澤的灰色背底上呈現(xiàn)出亮銀色的光澤斑,用砂紙打磨并重新腐蝕后偏析在原來(lái)位置又可重現(xiàn);還可以通過(guò)硬度試驗(yàn)進(jìn)行檢驗(yàn),因?yàn)槠鰠^(qū)與基體的硬度往往有較大差異。
鈦合金具有較高的缺陷敏感性,其中偏析出現(xiàn)的機(jī)率較高,通常這類缺陷能在原材料檢驗(yàn)或半成品檢驗(yàn)中發(fā)現(xiàn)。但由于低倍檢驗(yàn)取樣一般是取全橫截面試樣,而偏析有可能出現(xiàn)在材料的不同部位,這樣就有可能取不到偏析部位。這些缺陷可能會(huì)在生產(chǎn)加工、熱處理等過(guò)程中才暴露出來(lái),更多的是在成品零件經(jīng)腐蝕后進(jìn)行100%檢驗(yàn)時(shí)才能充分暴露出來(lái)。
裂紋的產(chǎn)生是由于原材料中存在著缺陷,即鈦錠熔煉時(shí)合金中混入了強(qiáng)烈氧化的富碳海綿鈦塊,發(fā)生了氧、碳元素偏聚。鈦棒在生產(chǎn)軋制時(shí),界面兩側(cè)的變形不協(xié)調(diào)導(dǎo)致局部應(yīng)力提高,從而引起開裂,在原材料出廠前又未車削干凈。為進(jìn)一步證實(shí)該判斷,實(shí)驗(yàn)檢查了庫(kù)房余料,在余料表面發(fā)現(xiàn)了裂紋。
3、結(jié)論
(1)鈦合金棒上的裂紋是由出廠時(shí)帶來(lái)的。原材料在冶煉過(guò)程中氧、碳含量偏高,聚集在材料中形成偏析,在軋制過(guò)程中界面兩側(cè)的變形不協(xié)調(diào)導(dǎo)致局部應(yīng)力提高,從而引起開裂。
(2)鈦錠熔煉時(shí)應(yīng)避免混入強(qiáng)烈氧化的海綿鈦塊。
相關(guān)鏈接