因?yàn)殁伜弯摰乃苄宰冃文芰蜔崤蛎浵禂?shù)相差較大,所以鈦和鋼的復(fù)合難度較大。目前,鈦/鋼復(fù)合板的主要制備方法有爆炸復(fù)合法、爆炸?軋制復(fù)合法、擴(kuò)散復(fù)合法和熱軋復(fù)合法。
1、爆炸復(fù)合法
爆炸復(fù)合法是以炸藥為能源,利用爆炸產(chǎn)生的沖擊力使兩層或者多層金屬板材發(fā)生劇烈碰撞、塑性變形、熔化以及原子間的互擴(kuò)散,實(shí)現(xiàn)界面牢固結(jié)合的一種金屬復(fù)合板制備方法。爆炸復(fù)合坯料的裝配方法有平行法和角度法兩種,平行法適用于大面積金屬復(fù)合板,角度法適用于高爆速炸藥和小面積金屬復(fù)合板,其裝配情況如下圖所示 。
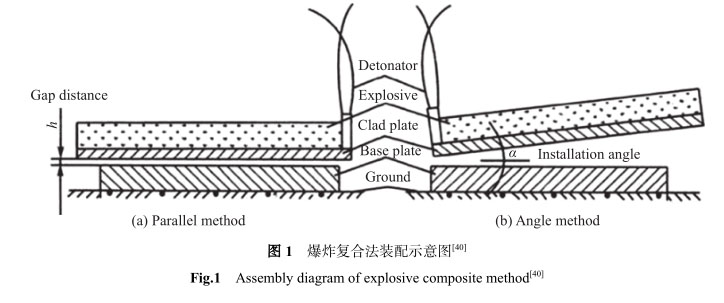
爆炸復(fù)合法制備的鈦/鋼復(fù)合板的界面呈連續(xù)而規(guī)則的波形,該波形由前渦和后渦組成。盡管波形界面組織的存在可改善鈦/鋼復(fù)合板沿爆炸方向的結(jié)合質(zhì)量,但波形前渦尖端易包裹Fe2、FeTi和 TiC 等金屬間化合物,這些金屬間化合物周圍常伴有微裂紋產(chǎn)生,會(huì)降低界面結(jié)合強(qiáng)度。
爆炸載荷對(duì)鈦/鋼復(fù)合板的界面結(jié)合強(qiáng)度、界面組織和金屬間化合物影響較大。 爆炸載荷較低時(shí),界面的波形平緩,振幅較小;隨著爆炸載荷增大,界面的波形振幅也逐漸增大,界面處熔化的金屬比例增大,界面結(jié)合更緊密;但增大爆炸載荷也會(huì)促使界面生成金屬間化合物,損害界面結(jié)合強(qiáng)度。
爆炸復(fù)合時(shí),界面碰撞的動(dòng)能損失和界面金屬間化合物的生成也會(huì)降低鈦/鋼復(fù)合板的界面結(jié)合強(qiáng)度. Manikandan等采用增加不同厚度過渡層金屬的方法控制爆炸復(fù)合時(shí)界面的能量損失,發(fā)現(xiàn)添加薄的過渡層金屬可產(chǎn)生沒有金屬間化合物的鈦/鋼界面,當(dāng)過渡層金屬厚度增大時(shí),界面金屬間化合物層的厚度也增大。
爆炸復(fù)合法因其工藝簡單,易復(fù)合性質(zhì)(熔點(diǎn)、強(qiáng)度、熱膨脹系數(shù)等)相差較大的鈦和鋼,是制備鈦/鋼復(fù)合板最常用的方法之一。但是,爆炸復(fù)合法因環(huán)境污染和無法連續(xù)化制備鈦/鋼復(fù)合板等問題,正在逐漸被軋制復(fù)合等其他方法所取代。
2、爆炸?軋制復(fù)合法
爆炸?軋制復(fù)合法是將待復(fù)合金屬板材通過爆炸復(fù)合后,再通過冷軋或熱軋獲得金屬復(fù)合板的一種制備方法. 爆炸?軋制復(fù)合法的一般工藝流程是:金屬板材準(zhǔn)備→表面處理→爆炸復(fù)合→爆后熱處理→熱軋→冷軋→校平. 由于爆炸復(fù)合鈦/鋼復(fù)合板的界面加工硬化會(huì)影響后續(xù)軋制效果,需要通過爆后熱處理消除界面的加工硬化;熱處理時(shí)需要控制溫度低于 850 ℃,避免界面生成Fe2Ti和 FeTi。鈦/鋼復(fù)合板的界面結(jié)合強(qiáng)度隨著軋制壓下率增大而增大, 這是因?yàn)殡S著軋制壓下率的增大,爆炸形成鈦/鋼復(fù)合板的波形界面逐漸變得平直,界面金屬間化合物破碎成不連續(xù)分布的狀態(tài),有利于界面結(jié)合強(qiáng)度的提高。王敬忠等先用爆炸復(fù)合法把鈦板和 DT4 純鐵過渡層復(fù)合,再用熱軋復(fù)合法將 Ti/DT4 與 Q235 鋼板復(fù)合,制備了 Ti/DT4/Q235 復(fù)合板;研究了制備工藝對(duì)界面結(jié)合強(qiáng)度的影響,發(fā)現(xiàn)熱軋溫度在 830~880 ℃、退火溫度在 550~650 ℃ 時(shí)界面金屬間化合物最少,界面結(jié)合強(qiáng)度可達(dá)250MPa。
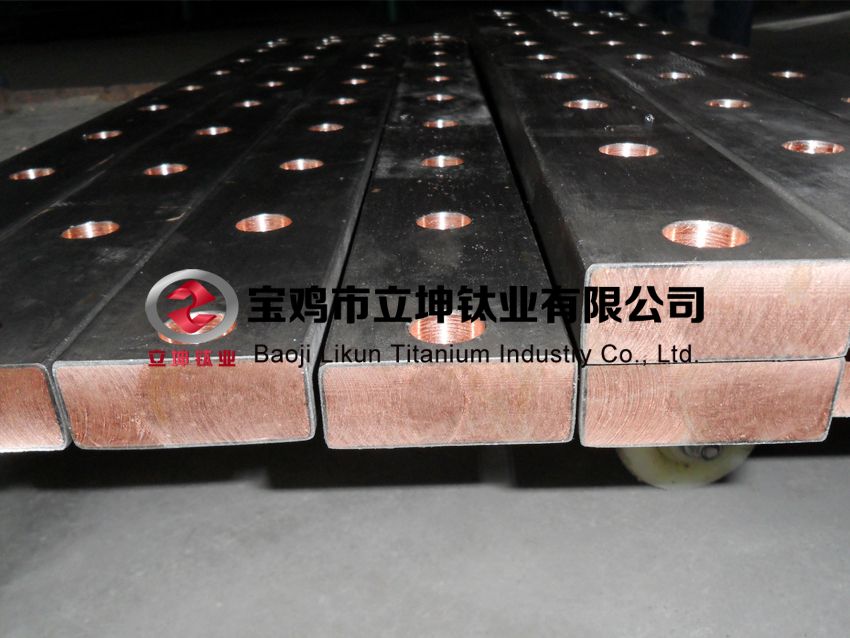
爆炸?軋制復(fù)合法不僅克服了爆炸復(fù)合法無法制備厚度小和表面質(zhì)量要求高的鈦/鋼復(fù)合板的缺點(diǎn),還解決了軋制復(fù)合法制備的鈦/鋼復(fù)合板存在的原材料及其尺寸受軋機(jī)能力限制等問題,極大地增加了制備的靈活性。但是,爆炸?軋制復(fù)合法依然存在環(huán)境污染和無法連續(xù)化制備鈦/鋼復(fù)合板等問題。
3、擴(kuò)散復(fù)合法
擴(kuò)散復(fù)合法是把表面清潔的金屬板材疊放在一起,然后加熱到一定溫度,同時(shí)加壓,通過原子間互擴(kuò)散使界面結(jié)合在一起的金屬復(fù)合板制備方法。采用擴(kuò)散復(fù)合法制備鈦/鋼復(fù)合板時(shí),通過加熱和加壓促進(jìn)界面原子互擴(kuò)散的同時(shí),也會(huì)促使界面生成 FeTi 等金屬間化合物,損害界面結(jié)合強(qiáng)度,為避免 FeTi 等的生成,擴(kuò)散復(fù)合時(shí)可通過在鈦層和鋼層中間添加銅 、鎳 、鋁 和鈮 等過渡層金屬,以此來顯著提高鈦/鋼復(fù)合板的界面結(jié)合強(qiáng)度. Kundu 等采用擴(kuò)散復(fù)合法在4MPa 壓力和 900 ℃ 溫度下制備了鈦/不銹鋼復(fù)合板,研究了保溫時(shí)間和鎳過渡層對(duì)界面結(jié)合強(qiáng)度的影響,發(fā)現(xiàn)鈦/鋼復(fù)合板的界面結(jié)合強(qiáng)度隨著保溫時(shí)間延長先增大后減小. 隨著保溫時(shí)間的延長,鈦/鋼復(fù)合板的界面原子擴(kuò)散越充分,冶金結(jié)合點(diǎn)越多,但界面金屬間化合物也逐漸增多,損害界面結(jié)合質(zhì)量;當(dāng)保溫時(shí)間為 2.7 ks 時(shí),界面結(jié)合強(qiáng)度最高達(dá)到 405 MPa. 增加鎳過渡層可避免界面生成 FeTi 等金屬間化合物,鈦/鋼復(fù)合板的界面結(jié)合強(qiáng)度最高可達(dá)479MPa。
擴(kuò)散復(fù)合法無污染,而且制備的鈦鋼復(fù)合板的界面殘余應(yīng)力小,不需要后續(xù)熱處理;但是制備效率低,可制備的鈦/鋼復(fù)合板尺寸受限,難以工業(yè)化推廣。
4、熱軋復(fù)合法
熱軋復(fù)合法是在軋機(jī)的強(qiáng)大壓力下,伴以熱作用,使組元金屬層的待復(fù)合表面破碎,并在整個(gè)金屬截面內(nèi)產(chǎn)生塑性變形,在破碎后露出的新鮮金屬表面形成組元金屬層間的機(jī)械嵌合和原子鍵合的一種高效金屬復(fù)合板制備方法. 因?yàn)殁伜弯摰乃苄宰冃文芰ο嗖钶^大,變形不協(xié)調(diào),為防止鈦/鋼復(fù)合板發(fā)生翹曲,提高成材率,一般采用對(duì)稱軋制,對(duì)稱軋制的組坯方法有 2 種,一種是按照鋼板→鈦板→隔離劑→鋼板的順序組坯,另一種是按照鋼板→鈦板→隔離劑→鈦板→鋼板的順序組坯。
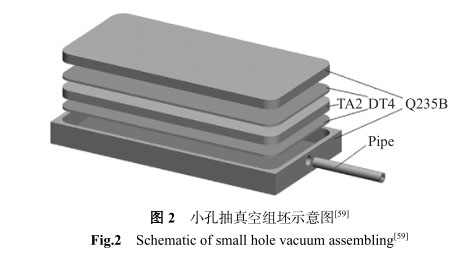
為避免高溫下鈦/鋼界面發(fā)生氧化,鈦/鋼組合坯料的待復(fù)合界面處需要保證真空,通常是在組坯時(shí)使界面實(shí)現(xiàn)真空然后再熱軋,常用的方法包括小孔抽真空法和真空電子束焊接法 。小孔抽真空法是先通過焊管向鈦/鋼組合坯料的待復(fù)合界面通入氬氣作為保護(hù)氣體,以防止焊接時(shí)坯料內(nèi)部因高溫發(fā)生氧化,然后用二氧化碳保護(hù)焊將組合坯料四周以及焊管與組合坯料連接處封嚴(yán),隨后用真空泵通過焊管將組合坯料內(nèi)部抽至真空后將焊管端部焊封,如圖 2 所示. 真空電子束焊接法是在高真空條件下對(duì)鈦/鋼組合坯料的待復(fù)合界面四周進(jìn)行電子束焊接封裝,以保證焊接、加熱及軋制過程中待復(fù)合界面的高真空。真空電子束焊接組坯熱軋復(fù)合過程如圖 3 所示. 小孔抽真空法的工藝簡單,制備成本低廉;但焊接過程在空氣環(huán)境中完成,鈦/鋼組合坯料的待復(fù)合界面在焊接過程中易氧化,且界面真空度不高,因此界面結(jié)合強(qiáng)度和成材率都較低. 真空電子束焊接法獲得的鈦/鋼組合坯料的待復(fù)合界面真空度高,界面質(zhì)量穩(wěn)定且結(jié)合強(qiáng)度高;但焊接設(shè)備造價(jià)和焊接工序成本都較高。
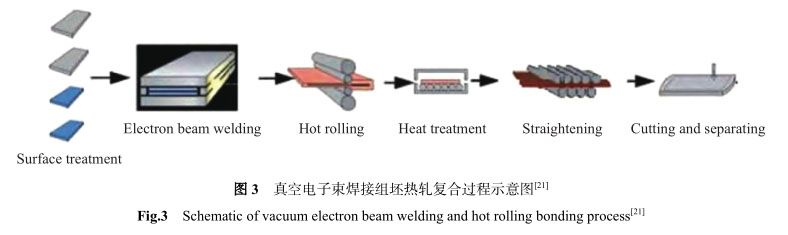
熱軋復(fù)合法的制備效率高,對(duì)環(huán)境無污染,可制備寬幅的鈦/鋼復(fù)合板,適合工業(yè)化應(yīng)用,但待復(fù)合界面需要在真空下熱軋復(fù)合,工藝較復(fù)雜,設(shè)備成本高。
相關(guān)鏈接